Maszyny pneumatyczne to urządzenia, które wykorzystują sprężone powietrze do wykonywania różnorodnych prac. Kluczowymi elementami ich budowy są kompresory, siłowniki, zawory oraz systemy sterowania. Kompresory odpowiadają za wytwarzanie sprężonego powietrza, które jest następnie kierowane do siłowników. Siłowniki przekształcają energię sprężonego powietrza w ruch mechaniczny, co pozwala na wykonanie pracy. Zawory kontrolują przepływ powietrza i ciśnienie w systemie, co jest niezwykle istotne dla prawidłowego funkcjonowania maszyny. Systemy sterowania, często oparte na nowoczesnych technologiach, umożliwiają precyzyjne zarządzanie pracą maszyny oraz jej parametrami. Warto również zwrócić uwagę na materiały używane do budowy tych urządzeń, które muszą być odporne na wysokie ciśnienie i korozję. Właściwy dobór materiałów oraz komponentów ma kluczowe znaczenie dla efektywności i trwałości maszyn pneumatycznych.
Jakie są zastosowania maszyn pneumatycznych w przemyśle
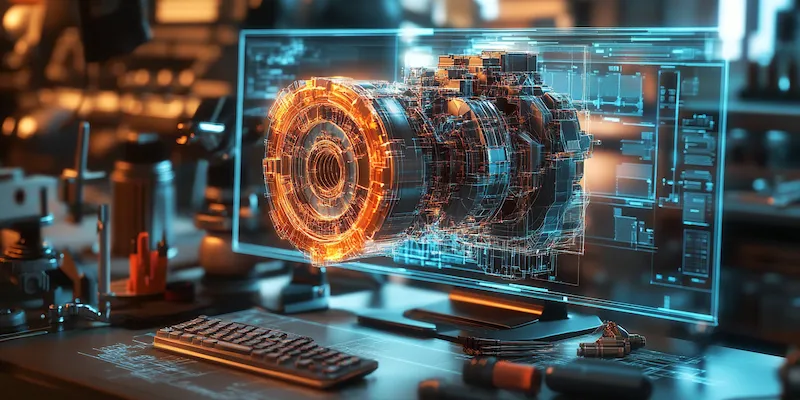
Budowa maszyn pneumatycznych
Maszyny pneumatyczne znajdują szerokie zastosowanie w różnych branżach przemysłowych, co czyni je niezwykle wszechstronnymi narzędziami. W przemyśle motoryzacyjnym wykorzystywane są do montażu i demontażu elementów pojazdów, a także do malowania i lakierowania. W branży spożywczej maszyny te służą do pakowania, transportu oraz napełniania produktów. Dzięki swojej precyzyjności i szybkości działania, maszyny pneumatyczne idealnie sprawdzają się w procesach wymagających dużej dokładności. W sektorze budowlanym używane są do podnoszenia ciężkich materiałów oraz w różnych pracach wykończeniowych. Również w medycynie znajdują zastosowanie w urządzeniach takich jak respiratory czy aparaty do znieczulenia. W każdym z tych przypadków kluczowe jest zapewnienie odpowiedniego ciśnienia oraz kontroli nad procesem, co pozwala na osiągnięcie optymalnych wyników.
Jakie są zalety i wady maszyn pneumatycznych
Maszyny pneumatyczne mają wiele zalet, które przyciągają uwagę inżynierów i menedżerów produkcji. Przede wszystkim charakteryzują się dużą niezawodnością oraz prostotą obsługi. Dzięki temu można je łatwo integrować z istniejącymi systemami produkcyjnymi. Kolejną zaletą jest ich wysoka prędkość działania, co przekłada się na zwiększenie wydajności procesów produkcyjnych. Maszyny te są również stosunkowo tanie w eksploatacji, ponieważ sprężone powietrze jest powszechnie dostępnym medium energetycznym. Niemniej jednak istnieją również pewne wady związane z ich użytkowaniem. Jednym z głównych problemów jest konieczność utrzymania odpowiedniego ciśnienia powietrza, co może wiązać się z dodatkowymi kosztami związanymi z konserwacją kompresorów i systemów filtracyjnych. Ponadto maszyny pneumatyczne mogą być mniej precyzyjne niż ich elektryczne odpowiedniki w niektórych zastosowaniach wymagających dużej dokładności.
Jakie są nowoczesne technologie w budowie maszyn pneumatycznych
W ostatnich latach nastąpił znaczny rozwój technologii związanych z budową maszyn pneumatycznych, co przyczyniło się do ich większej efektywności i wszechstronności. Nowoczesne rozwiązania obejmują zastosowanie inteligentnych systemów sterowania, które umożliwiają automatyzację procesów oraz monitorowanie parametrów pracy maszyn w czasie rzeczywistym. Dzięki temu możliwe jest szybkie reagowanie na zmiany warunków pracy oraz optymalizacja procesów produkcyjnych. Również materiały używane do budowy komponentów maszyn uległy znacznemu ulepszeniu – obecnie stosuje się lekkie i wytrzymałe tworzywa sztuczne oraz stopy metali o wysokiej odporności na korozję i zużycie. Dodatkowo rozwój technologii sensorowych pozwala na lepsze monitorowanie stanu technicznego maszyn oraz przewidywanie awarii przed ich wystąpieniem. To wszystko sprawia, że nowoczesne maszyny pneumatyczne stają się bardziej niezawodne i efektywne, a ich zastosowanie staje się coraz szersze w różnych branżach przemysłowych.
Jakie są kluczowe aspekty konserwacji maszyn pneumatycznych
Konserwacja maszyn pneumatycznych jest niezbędnym elementem ich prawidłowego funkcjonowania oraz długowieczności. Regularne przeglądy i utrzymanie w dobrym stanie technicznym poszczególnych komponentów mogą znacząco wpłynąć na efektywność pracy całego systemu. Kluczowym aspektem konserwacji jest kontrola stanu kompresorów, które odpowiadają za wytwarzanie sprężonego powietrza. Należy regularnie sprawdzać poziom oleju, filtry oraz szczelność układu, aby uniknąć niepożądanych strat ciśnienia. Również siłowniki wymagają szczególnej uwagi – ich uszczelnienia powinny być regularnie wymieniane, aby zapobiec wyciekom powietrza. Zawory powinny być czyszczone i smarowane, aby zapewnić ich płynne działanie. Warto również zwrócić uwagę na systemy filtracyjne, które chronią maszyny przed zanieczyszczeniami. Zanieczyszczone powietrze może prowadzić do awarii i obniżenia wydajności. Oprócz regularnych przeglądów, istotne jest także szkolenie pracowników w zakresie obsługi i konserwacji maszyn pneumatycznych, co pozwoli na szybsze wykrywanie problemów oraz ich skuteczne rozwiązywanie.
Jakie są różnice między maszynami pneumatycznymi a hydraulicznymi
Maszyny pneumatyczne i hydrauliczne to dwa różne typy urządzeń, które wykorzystują różne media do wykonywania pracy mechanicznej. Główna różnica polega na tym, że maszyny pneumatyczne operują na sprężonym powietrzu, podczas gdy maszyny hydrauliczne korzystają z cieczy, najczęściej oleju hydraulicznego. Ta fundamentalna różnica wpływa na sposób działania obu typów maszyn oraz ich zastosowanie w różnych branżach przemysłowych. Maszyny pneumatyczne charakteryzują się szybszym czasem reakcji oraz mniejszą wagą, co czyni je idealnymi do zastosowań wymagających dużej prędkości i mobilności. Z drugiej strony maszyny hydrauliczne oferują większą siłę i precyzję, co sprawia, że są bardziej odpowiednie do ciężkich prac budowlanych czy przemysłowych. W kontekście kosztów eksploatacji, maszyny pneumatyczne są zazwyczaj tańsze w utrzymaniu ze względu na niższe koszty energii oraz prostszą konstrukcję. Jednakże w przypadku zastosowań wymagających dużych obciążeń lepszym wyborem mogą być maszyny hydrauliczne.
Jakie są przyszłe trendy w rozwoju technologii maszyn pneumatycznych
Przemysł 4.0 oraz rozwój technologii cyfrowych mają ogromny wpływ na przyszłość maszyn pneumatycznych. W nadchodzących latach można spodziewać się dalszej automatyzacji procesów produkcyjnych oraz integracji maszyn z systemami zarządzania danymi. Internet rzeczy (IoT) umożliwi monitorowanie stanu technicznego maszyn w czasie rzeczywistym, co pozwoli na szybsze reagowanie na potencjalne awarie oraz optymalizację procesów produkcyjnych. Wprowadzenie sztucznej inteligencji do systemów sterowania może przyczynić się do jeszcze większej efektywności działania maszyn pneumatycznych poprzez analizę danych i prognozowanie potrzeb produkcyjnych. Również rozwój materiałów kompozytowych oraz nanotechnologii wpłynie na konstrukcję komponentów maszyn, co pozwoli na zwiększenie ich wytrzymałości oraz redukcję wagi. Warto również zauważyć rosnącą tendencję do stosowania energii odnawialnej w procesach produkcyjnych, co może wpłynąć na sposób zasilania kompresorów i innych urządzeń pneumatycznych.
Jakie są najczęstsze problemy związane z użytkowaniem maszyn pneumatycznych
Użytkowanie maszyn pneumatycznych wiąże się z pewnymi wyzwaniami, które mogą wpływać na ich wydajność oraz niezawodność. Jednym z najczęstszych problemów jest niewłaściwe ciśnienie powietrza w systemie, które może prowadzić do spadku efektywności pracy lub nawet uszkodzenia komponentów maszyny. Zbyt niskie ciśnienie może skutkować wolniejszym działaniem siłowników, podczas gdy zbyt wysokie ciśnienie może prowadzić do awarii zaworów czy uszczelnień. Kolejnym powszechnym problemem są wycieki powietrza, które mogą występować w różnych częściach układu pneumatycznego. Wycieki te nie tylko obniżają wydajność maszyny, ale również zwiększają koszty eksploatacji związane z koniecznością dostarczania dodatkowego sprężonego powietrza. Problemy z filtracją powietrza to kolejny istotny aspekt – zanieczyszczone powietrze może prowadzić do uszkodzeń wewnętrznych komponentów maszyny oraz obniżenia jakości produkcji.
Jakie są różnice między siłownikami pneumatycznymi a elektrycznymi
Siłowniki pneumatyczne i elektryczne to dwa popularne rozwiązania stosowane w automatyce przemysłowej, jednak różnią się one zasadniczo pod względem działania i zastosowania. Siłowniki pneumatyczne wykorzystują sprężone powietrze do generowania ruchu liniowego lub obrotowego, co czyni je idealnymi do aplikacji wymagających dużej prędkości działania oraz prostoty konstrukcji. Z kolei siłowniki elektryczne działają na zasadzie przekształcania energii elektrycznej w ruch mechaniczny za pomocą silników elektrycznych i przekładni. Siłowniki elektryczne oferują większą precyzję ruchu oraz łatwiejszą kontrolę nad parametrami pracy dzięki zastosowaniu nowoczesnych systemów sterowania. W kontekście kosztów eksploatacji siłowniki pneumatyczne są zazwyczaj tańsze w utrzymaniu ze względu na niższe koszty energii związane z użyciem sprężonego powietrza. Jednakże siłowniki elektryczne często charakteryzują się wyższą efektywnością energetyczną i mniejszym zużyciem energii przy długotrwałym użytkowaniu.
Jakie są kluczowe czynniki wpływające na wybór maszyn pneumatycznych
Wybór odpowiednich maszyn pneumatycznych do konkretnego zastosowania wymaga uwzględnienia wielu czynników, które mogą wpływać na efektywność pracy oraz koszty eksploatacji urządzeń. Przede wszystkim należy określić wymagania dotyczące wydajności – ilość sprężonego powietrza potrzebna do wykonania określonych zadań ma kluczowe znaczenie dla wyboru odpowiedniego kompresora oraz siłowników. Kolejnym istotnym czynnikiem jest rodzaj medium roboczego – różne aplikacje mogą wymagać różnych parametrów ciśnienia i temperatury sprężonego powietrza, co powinno być brane pod uwagę podczas projektowania systemu pneumatycznego. Ważne jest również uwzględnienie warunków środowiskowych, w jakich będą pracować maszyny – obecność zanieczyszczeń czy wilgoci może wpłynąć na trwałość komponentów oraz konieczność stosowania dodatkowych filtrów czy osuszaczy powietrza.